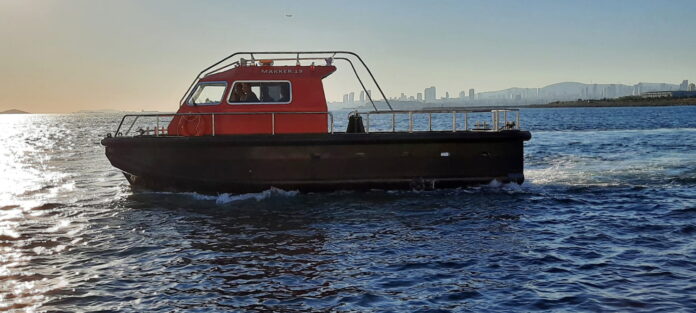
Die Schramm-Gruppe hat einen neuen Werkstoff entdeckt: Der Kunststoff HD-PE ist leicht, beständig und vor allem kostengünstig. Ein Festmacherboot ist als Pilotprojekt bereits im Wasser. Aber auch in der Binnenschifffahrt könnten sich große Chancen ergeben
Makker 19 –so heißt das 9,90 m lange und 3,80 m breite Festmacherboot, das für die Schramm group auf einer Werft in der Türkei gebaut wurde und demnächst in Dienst gestellt werden soll. Das Besondere ist das Material: Der Rumpf besteht aus HD-PE einem stress- und stoßfesten Kunststoff, der sonst beim Bau von druckbeständigen Gas- und Wasserleitungen eingesetzt wird. Es soll nicht nur ein älteres Vorgängermodell ersetzen. »Es ist ein völlig anderes, viel besseres Schiff«, sagt Hans Helmut Schramm.
Alle bisherigen Festmacherboote sind aus Stahl und mit nur einem Motor ausgestattet. In anspruchsvollen Revieren wie der Unterelbe und im Hamburger Hafen mit ordentlich Wind, Strömung, Schwell und immer größeren Schiffen durchaus ein mögliches Problem bei einem Maschinenausfall. Doch die Boote waren bislang zu klein, um einen zweiten Motor einzubauen. »Also haben wir seit zwei Jahren überlegt, wie wir es besser machen können«, so Schramm.
Auf einer türkischen Werft hatte das Unternehmen ein anderes, größeres Schiff in Auftrag gegeben. Dabei weckten Seebojen aus HD-PE die Aufmerksamkeit der Brunsbütteler. Die zeigten auch nach Jahren im Einsatz keinerlei Verschleiß. So entstand die Idee, auch Schiffe aus diesem Kunststoff zu fertigen.
Entwurf stammt von NavConsult
Die unternehmenseigene Design- und Konstruktionsfirma NavConsult lieferte die Entwürfe für eine Bootshülle in Sandwich-Bauweise in Doppelhülle, die mit festem Schaum gefüllt ist und das Boot unsinkbar macht. Bei Crashtests durch Auffahren auf Geröll und Felsen entstanden lediglich beulenartige Verformungen, die durch erneutes Erwärmen des Kunststoffs ohne großen Aufwand repariert werden konnten.
Die größten Vorteile des bis zu 22 kn schnellen Bootes aber sind das geringere Gewicht von 300 kg/m3 gegenüber Stahl mit 7 t/m3 hat und die geringeren Kosten sowie die um rund 20% geringeren Kosten. Dadurch kann der Tiefgang der schwimmenden Einheiten erheblich reduziert werden, konkret auf 0,80 m.
HD-PE sei lebensmittelecht, könne umweltfreundlich recycelt werden und brauche keine Wartung durch neue Farbanstriche, wodurch auch Betriebskosten gespart werden könnten. Letztlich sei auch die CO2-Bilanz deutlich besser als bei Stahl.
Außerdem wurde dank des leichteren Entwurfs das Ziel erreicht, zwei Motoren einzubauen und die gewünschte Redundanz zu erreichen. Schramm hat sich bei seinem ersten Boot für zwei Cummins à 250 PS entschieden, die über ein ZF-Getriebe und eine gewöhnliche Welle einen Standard-Festpropeller antreiben. »Künftig wollen wir den deutschen und europäischen Markt für dieses neue Baumaterial begeistern«, sagt der Unternehmenschef.
Vermarktung soll jetzt starten
Die Gruppe hat sich die exklusiven Vermarktungsrechte für diesen neuen Schiffstyp in Europa gesichert. Die türkische Partnerwerft könne ab Oktober bis zu zehn Einheiten in unterschiedlichen Ausführungen und mit SOLAS-konformer Technik an Bord pro Jahr bauen. Kosten: 310.000–350.000 €. Der Entwurf eigne sich nicht nur als Festmacherboot, sondern auch als Service-Einheit für die Offshore-Industrie oder für die Wasserschutzpolizei und andere Behördenschiffe. Das eigentliche Problem, berichtet Schramm, sei die Zulassung. »Alles, was von Normen und Vorgaben abweicht, ist schwierig umzusetzen«, sagt er. Im Schiffbau gebe es derzeit eben nur Stahl, Alu und Holz, aber keinen Kunststoff wie HD-PE. Letztlich will die See BG das neue Boot zulassen, weil es unter 10 m lang ist und die italienische Klassifikationsgesellschaft RINA die nötigen Stabilitäts- und Festigkeitsberechnungen vorgelegt hat.
Potenzial für Binnenschiffe
Dabei sieht Hans Helmut Schramm, dessen Unternehmensgruppe Häfen, eine Schlepp- und Bergungsreederei und eine eigene Schiffbauabteilung betreibt, großes Potenzial für diesen Werkstoff, gerade auch in der Binnenschifffahrt.
Einen Euro-I-Leichter aus dem elastischen und hoch festen Kunststoff für eine Zuladung von 80–100 t hat Schramm für den Einsatz im Hamburger Hafen bereits in Planung. Der Tiefgang läge bei lediglich 0,14 m. Ein vergleichbares Konstrukt aus Stahl würde schon ohne Zuladung so tief im Wasser liegen. »Wir könnten also 20% bis 25% mehr an Gütern gegenüber einem Stahlbau transportieren. Das wäre doch eine Lösung für das zunehmende Risiko von Niedrigwasser«, sagt Schramm.
Für lange Einheiten sei HD-PE erst einmal zu »weich«. Da der form- und schweißbare Kunststoff aber wie Stahl mit Spanten und Wanten verarbeitet werden könne, sei er auch für den Bau von größeren Binnenschiffen oder Schubbooten geeignet und könnte daher den Schiffbau geradezu revolutionieren. Technisch sei das bei geringeren Kosten machbar. »Wir haben Zeichnungen für ganz verschiedene Schiffstypen in der Schublade«, sagt Schramm.
»Aber wir müssen noch Erfahrungen sammeln und vermutlich viel Überzeugungsarbeit leisten«, räumt Schramm ein. Denn für einen flächendeckenden Einsatz des neuen Werkstoffs müssten die entsprechenden Verordnungen und Zulassungskriterien bei den Genehmigungsbehörden geändert werden. Er hofft jetzt auf die Politik, die die Weichen stellen müsse, um HD-PE in die Praxisanwendung zu bringen. »Wir als Unternehmen sind jedenfalls bereit, voranzugehen und zu investieren«, betont er.