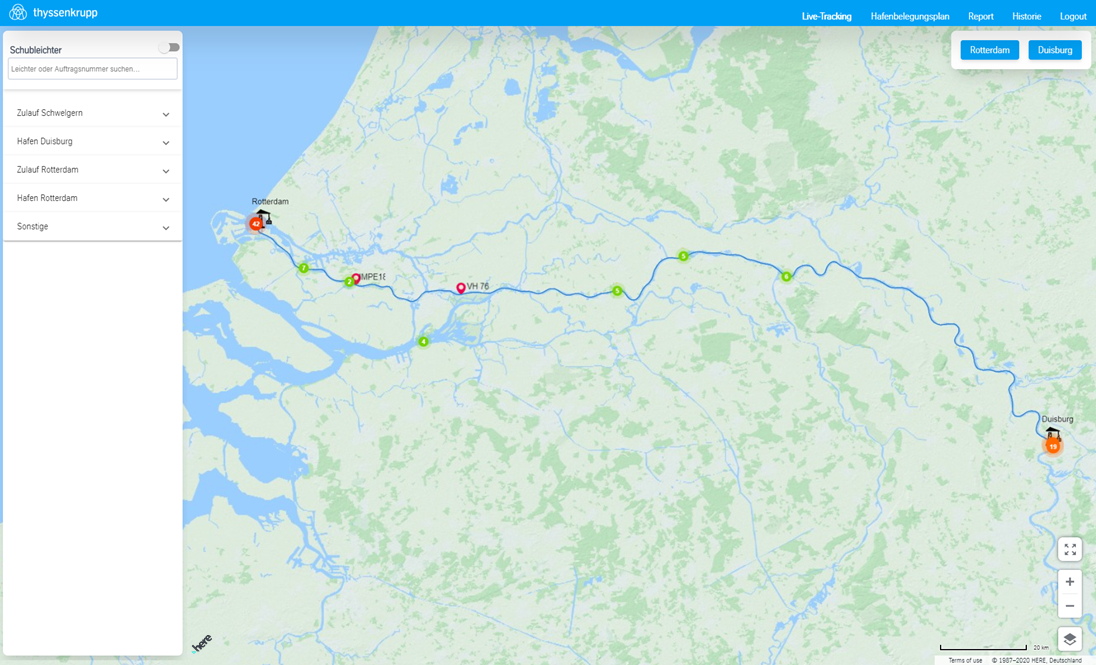
Rund 240 km sind es mit dem Schiff über den Rhein vom Europoort Rotterdam bis zum Hüttenwerk von thyssenkrupp Steel in Duisburg. Die Wasserachse spielt bei der Rohstoffversorgung des Werks eine wichtige Rolle und der direkte Weg ist ein entscheidender Standortvorteil: Bis zu 10.000 Schubleichter, die auf 75 m Länge mit bis zu 2.700 t beladen werden können, beliefern den Werkhafen mit Eisenerz, Kohle sowie weiteren Rohstoffen.
Diese Vielzahl von schwimmenden Einheiten muss gut koordiniert werden, denn der Platz in den Werkshäfen Walsum und Schwelgern ist begrenzt. Zudem ist Logistik oft nur mit kurzem Vorlauf planbar: Unwetter oder schlechte Sicht durch Nebel können genauso zu Verzögerungen führen wie ein niedriger Rheinpegel. Auch Wartungen an den Hochöfen senken vorübergehend den Materialbedarf.
Im Zuge der Digitalisierungsstrategie optimiert thyssenkrupp Steel die Leichterkoordination mit moderner Sensortechnologie. »Unser Ziel war daher eine smarte digitale Lösung, mit der alle Prozesspartner Zugriff auf ein Live-Abbild der Lieferkette erhalten«, erklärt Walter Scheider von der thyssenkrupp Steel Logistik.
In der Folge ist nun jeder Leichter mit einem solarbetriebenen GPS-Sensor ausgestattet. Das Ergebnis ist eine digitale Landkarte, auf der alle Beteiligten jeden einzelnen Leichter zu jeder Zeit im Blick behalten können – inklusive Informationen zur Tonnage, dem geladenen Rohstoff und mittels künstlicher Intelligenz (KI) berechneter Ankunftszeit im Zielhafen. Dadurch werden Zeit und Kosten gespart. So kann ein Schiffsführer auf dem Weg nach Duisburg langsamer und spritsparender fahren, wenn ohnehin absehbar ist, dass vor dem Werkhafen auf Einfahrt gewartet werden müsste. »Durch die Live-Verfolgung können wir deutlich besser im Voraus planen«, erklärt Christoph Pohl, zuständig für den Rohstoffumschlag in den thyssen-Werkhäfen.